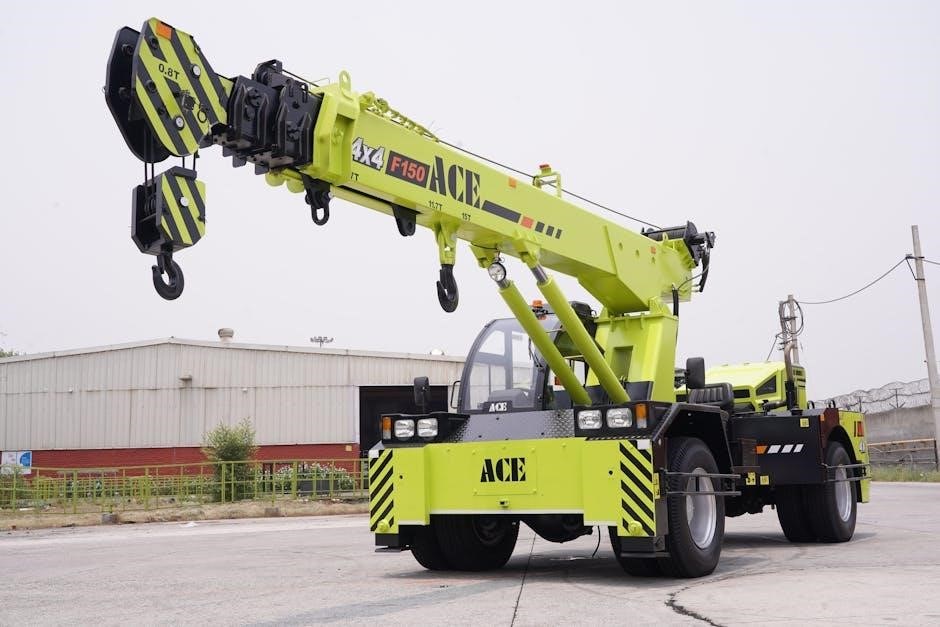
ASTM B633 provides specifications for electrodeposited zinc coatings on iron and steel, ensuring corrosion protection and durability․ It covers thickness classes, finishes, and compliance requirements․
Overview of the Standard
ASTM B633 outlines requirements for electrodeposited zinc coatings on iron and steel to provide corrosion protection․ It specifies material and process standards, including coating thickness, adhesion, and supplementary finishes․ The standard ensures coatings meet durability and performance criteria, addressing environmental factors and compliance with regulations like RoHS․ Widely adopted, it serves as a critical guide for manufacturers to achieve high-quality, corrosion-resistant products, essential for industries relying on steel and iron components․
Importance of ASTM B633 in Corrosion Protection
ASTM B633 is crucial for ensuring effective corrosion protection of iron and steel through electrodeposited zinc coatings․ It establishes standardized thickness and finish requirements, enhancing durability and resistance to environmental degradation․ By adhering to this standard, manufacturers can produce components with extended lifespans, reducing maintenance and replacement costs․ Its guidelines are vital for industries like construction and automotive, where corrosion resistance is paramount, ensuring reliability and safety in critical applications․
Scope and Purpose of ASTM B633
ASTM B633 covers material and process requirements for electrodeposited zinc coatings on iron and steel, ensuring corrosion protection and product quality through standardized specifications․
Materials Covered Under the Standard
ASTM B633 applies to electrodeposited zinc coatings on iron and steel articles, including carbon steel, stainless steel, and alloy steel products․ It specifies requirements for coatings on bolts, nuts, and other hardware․ The standard covers materials like carbon steel, stainless steel, and alloy steel products․ It excludes electrodeposited zinc-coated steel wire or sheets, which are addressed in other ASTM standards․ The specification ensures coatings meet requirements for corrosion protection, durability, and adherence to international standards like AISI, ISO, BS, and SAE․
Purpose of Electrodeposited Zinc Coatings
Electrodeposited zinc coatings are applied to iron and steel articles to provide corrosion protection, enhancing durability and extending lifespan․ They create a sacrificial barrier, protecting the base metal from environmental degradation․ The coatings are ideal for use in harsh conditions, including atmospheric and humid environments․ Their purpose is to ensure long-term protection while maintaining surface integrity․ This method is widely recognized for its effectiveness and is specified in ASTM B633 to meet industry standards for reliability and performance in various applications․
Key Classifications in ASTM B633
ASTM B633 defines four primary coating classifications: Fe/Zn 4, Fe/Zn 8, Fe/Zn 12, and Fe/Zn 25, each specifying distinct thickness requirements for zinc coatings․
- Fe/Zn 4
- Fe/Zn 8
- Fe/Zn 12
- Fe/Zn 25
Fe/Zn 4 Classification
The Fe/Zn 4 classification in ASTM B633 represents the thinnest electrodeposited zinc coating, typically ranging from 0․2 to 0․6 mils (5 to 15 micrometers)․ This class is ideal for small parts or components where minimal coating thickness is required but still provides adequate corrosion protection․ It is often used in applications where size and weight constraints are critical․ The Fe/Zn 4 classification balances cost-effectiveness with basic corrosion resistance, making it suitable for less demanding environments․ Its specifications ensure consistency and reliability in industrial applications․
Fe/Zn 8 Classification
The Fe/Zn 8 classification in ASTM B633 specifies a medium-thickness electrodeposited zinc coating, typically 0․8 mils (20 micrometers), offering enhanced corrosion protection compared to Fe/Zn 4․ This class is widely used for parts exposed to moderate environmental conditions, balancing durability and cost-effectiveness․ It is ideal for industrial applications where higher corrosion resistance is necessary without excessive coating thickness․ The Fe/Zn 8 classification ensures compliance with RoHS standards, making it suitable for manufacturing and construction industries requiring reliable, long-lasting protection for steel components․
Fe/Zn 12 Classification
The Fe/Zn 12 classification in ASTM B633 refers to electrodeposited zinc coatings with a thickness of 1․2 mils (30 micrometers), offering superior corrosion protection․ This class is designed for applications in harsh environments, ensuring long-term durability․ It is commonly used in industries like automotive and construction, where parts are exposed to severe conditions․ The Fe/Zn 12 coating provides excellent resistance to rust and wear, making it a reliable choice for critical components requiring extended lifespan and minimal maintenance․ Its thickness ensures enhanced protection without being excessive for typical industrial needs․
Fe/Zn 25 Classification
The Fe/Zn 25 classification in ASTM B633 specifies electrodeposited zinc coatings with a thickness of 2․5 mils (64 micrometers)․ This is the thickest coating class, designed for extreme environmental conditions․ It provides exceptional corrosion resistance and durability, making it ideal for heavy-duty applications in industries like construction and automotive․ The Fe/Zn 25 coating ensures long-term protection against severe corrosion and wear, particularly in outdoor or high-humidity environments․ Its robustness makes it suitable for structural components requiring maximum protection and extended lifespan․
Supplementary Finishes
Supplementary finishes enhance coating properties like corrosion resistance and adhesion․ ASTM B633 includes types SC1 to SC5, offering options for chromate conversion, phosphate, and other treatments to improve durability․
Types of Supplementary Finishes
ASTM B633 defines five types of supplementary finishes: SC1 (chromate conversion coating), SC2 (phosphate coating), SC3 (organic coating), SC4 (dry lubricant), and SC5 (combination of SC1 and SC4)․ These finishes enhance properties like corrosion resistance, adhesion, and lubricity․ SC1 provides a protective chromate layer, while SC2 improves paint adhesion․ SC3 adds an organic topcoat for extra protection․ SC4 incorporates dry lubricants for wear resistance, and SC5 combines SC1 and SC4 for enhanced performance․ These finishes cater to specific industrial needs, ensuring coatings meet diverse application requirements․
Thickness Requirements
ASTM B633 specifies minimum and maximum coating thicknesses for electrodeposited zinc coatings, ensuring durability and corrosion protection․ The standard covers Fe/Zn 4, 8, 12, and 25 classifications․
Minimum and Maximum Coating Thickness
ASTM B633 defines specific thickness requirements for electrodeposited zinc coatings, categorized into four classes: Fe/Zn 4, Fe/Zn 8, Fe/Zn 12, and Fe/Zn 25․ The Fe/Zn 4 class specifies a minimum thickness of 0․2 mils (5 μm) and a maximum of 0․6 mils (15 μm), suitable for small parts․ Fe/Zn 8 ranges from 0․4 mils (10 μm) to 1․2 mils (30 μm), ideal for general applications․ Fe/Zn 12 requires 0․6 mils (15 μm) to 1․8 mils (45 μm), while Fe/Zn 25 mandates a minimum of 1․0 mil (25 μm) and a maximum of 2․5 mils (63 μm) for harsh environments․ These specifications ensure optimal corrosion protection without excessive material usage․
Test Methods for Coating Properties
ASTM B633 outlines test methods for evaluating coating properties, including adhesion, corrosion resistance, and thickness measurement․ These tests ensure coatings meet specified durability and performance standards․
Adhesion Testing
Adhesion testing ensures electrodeposited zinc coatings bond securely to the substrate․ Methods include tape tests and scribe tests to measure the coating’s resistance to separation․ These tests are critical for verifying the coating’s durability under various environmental conditions․ Proper adhesion prevents delamination, ensuring long-term corrosion protection and structural integrity․ ASTM B633 specifies procedures to evaluate adhesion, guaranteeing coatings meet performance standards․ Failure to meet these criteria can result in premature coating failure, compromising the material’s protective properties․
Corrosion Resistance Testing
Corrosion resistance testing evaluates the durability of zinc coatings in various environments․ ASTM B633 specifies methods like salt spray testing to assess how well coatings withstand corrosion․ These tests determine the coating’s performance in outdoor, indoor, and corrosive settings․ The results help ensure the coatings meet specified standards for protecting iron and steel․ Testing data from worldwide studies provides comparative insights into the corrosion behavior of electrodeposited zinc․ This ensures the coatings offer reliable, long-term protection against environmental degradation․
Thickness Measurement
Thickness measurement is critical to ensure coatings meet ASTM B633 requirements․ The standard specifies methods like micrometers or X-ray fluorescence for accurate thickness assessment․ Coatings are classified into four thickness categories: Fe/Zn 4, 8, 12, and 25, representing minimum thickness in micrometers․ These measurements ensure compliance with specified standards and guarantee the desired corrosion protection and durability․ Proper thickness verification is essential for quality control and to confirm the coating’s suitability for its intended application․
Compliance and Certification
Compliance and certification ensure electrodeposited zinc coatings meet ASTM B633 standards․ RoHS compliance guarantees environmental safety, with certification involving rigorous testing and detailed documentation processes․
RoHS Compliance
ASTM B633 ensures electrodeposited zinc coatings comply with RoHS regulations, restricting hazardous substances like lead, mercury, and cadmium․ Compliance verification involves rigorous testing and documentation to meet global environmental standards, ensuring safer and more sustainable products․ This requirement is critical for manufacturers to adhere to international regulations and promote eco-friendly practices across industries․ RoHS compliance in ASTM B633 is essential for suppliers and end-users seeking to align with environmental goals and legal obligations, fostering trust and reliability in coated products․
Certification Process
The certification process for ASTM B633 involves rigorous testing and documentation to ensure compliance with specified standards․ Manufacturers must submit their electrodeposited zinc coatings for evaluation, including thickness, adhesion, and corrosion resistance tests․ Test results are reviewed and validated by accredited laboratories․ Once requirements are met, a certification is issued, confirming the product’s adherence to ASTM B633․ Regular audits ensure ongoing compliance, maintaining trust and quality assurance for coated products across industries․ This process is essential for verifying the integrity and reliability of zinc-coated materials․
Applications and Uses
ASTM B633 is widely applied in industrial and structural steel sectors, protecting components from corrosion․ It’s used for automotive, construction, and machinery parts, ensuring durability and longevity․
Industrial Applications
ASTM B633 is extensively used in various industries to protect steel components from corrosion․ It is commonly applied in automotive manufacturing, construction, and machinery production․ The standard ensures durability and longevity of parts exposed to harsh environments․ Industrial applications include fasteners, beams, and machinery components․ The coatings are particularly effective in marine and outdoor settings, where corrosion resistance is critical․ By adhering to ASTM B633, manufacturers ensure high-quality, reliable products that meet international standards, making it a cornerstone for industrial corrosion protection solutions․
Structural Steel Applications
ASTM B633 plays a vital role in structural steel applications, ensuring long-term corrosion protection in construction and infrastructure projects․ Zinc coatings adhering to this standard are widely used for steel beams, columns, and frameworks exposed to harsh environments․ The Fe/Zn 12 classification is particularly favored for structural components due to its durability and resistance to rust․ These coatings are essential for maintaining the integrity of steel structures in outdoor and marine settings, ensuring safety and extending service life in critical infrastructure applications․
Advantages of ASTM B633 Coatings
ASTM B633 coatings offer superior corrosion protection, durability, and cost-effectiveness for iron and steel components․ They ensure long-term performance and compliance with environmental regulations like RoHS․
Cost-Effectiveness
ASTM B633 coatings are highly cost-effective, offering long-term corrosion protection and reducing maintenance costs․ They provide a durable barrier against rust and environmental factors, minimizing the need for frequent repairs or replacements․ The standard’s flexibility in coating thickness and finishes allows for tailored applications, optimizing expenses without compromising performance․ This makes ASTM B633 an economical choice for industries seeking reliable, long-lasting corrosion protection while maintaining budget efficiency․
Durability
ASTM B633 ensures the durability of zinc coatings on iron and steel by providing a robust protective barrier against rust and environmental factors․ The standard’s Fe/Zn classifications, such as Fe/Zn 4 and Fe/Zn 12, specify coating thicknesses that enhance longevity․ These coatings are designed to withstand harsh conditions, offering long-term protection that reduces the need for frequent maintenance․ This durability makes ASTM B633 coatings a reliable choice for industries requiring extended material lifespan․
Historical Background and Development
ASTM B633 was first published in 1985 to standardize electrodeposited zinc coatings, evolving over time to include advancements in materials and testing methodologies․
Evolution of Zinc Coating Standards
Zinc coating standards have evolved significantly since their inception, with ASTM B633 emerging as a key specification․ Initially developed in 1985, it addressed electrodeposited zinc coatings on iron and steel, focusing on corrosion protection․ Over time, the standard has been updated to incorporate advancements in materials science, testing methods, and environmental considerations․ Revisions include improved thickness specifications, supplementary finishes, and compliance with regulations like RoHS․ These updates ensure the standard remains a benchmark for quality and durability in corrosion protection applications․
Sources for ASTM B633 PDF
The ASTM B633 PDF can be purchased from the official ASTM website or authorized distributors, ensuring access to the latest updates and compliance requirements․
Official ASTM Website
The official ASTM website is the primary and most reliable source to obtain the ASTM B633 PDF․ It provides direct access to the standard, ensuring the document is up-to-date and compliant with the latest revisions․ Users can purchase the PDF with options for multi-user access and printable rights, making it ideal for organizations and professionals․ The website also offers detailed descriptions, scope, and related standards, ensuring clarity and ease of access for those seeking the specification․
Authorized Distributors
Authorized distributors offer reliable access to the ASTM B633 PDF, ensuring authenticity and compliance with the latest standards․ These distributors provide secure and efficient ways to purchase the document, often with options for multi-user licenses and downloadable formats․ They may also offer additional resources, such as related standards or technical support, to assist with implementation․ Purchasing from authorized distributors guarantees access to the most current version of the specification, essential for maintaining compliance and quality in industrial applications․
ASTM B633 is a critical standard for corrosion protection, offering comprehensive guidelines for electrodeposited zinc coatings․ Its specifications ensure durability and reliability in various industrial applications, making it indispensable for manufacturers and industries worldwide․
ASTM B633 provides specifications for electrodeposited zinc coatings on iron and steel, ensuring corrosion protection․ It includes four thickness classes, supplementary finishes, and RoHS compliance․ The standard outlines material and process requirements, test methods, and certification processes․ Widely used in industrial and structural applications, it ensures durability and reliability․ The ASTM B633 PDF is available through official sources, offering comprehensive guidelines for manufacturers and industries seeking to enhance product lifespan and performance through high-quality zinc coatings․
References
Related standards include ASTM B632, B631, and B841, which support electrodeposited zinc coating specifications, providing complementary guidelines for materials and processes․
Related ASTM Standards
ASTM B633 is complemented by other standards like ASTM B632 and ASTM B631, which address zinc-nickel coatings and zinc coatings on stainless steel, respectively․ Additionally, ASTM B841 provides specifications for post-treatment of zinc coatings to enhance corrosion resistance․ Together, these standards ensure comprehensive protection and quality for coated products, offering detailed guidelines for various applications and materials․